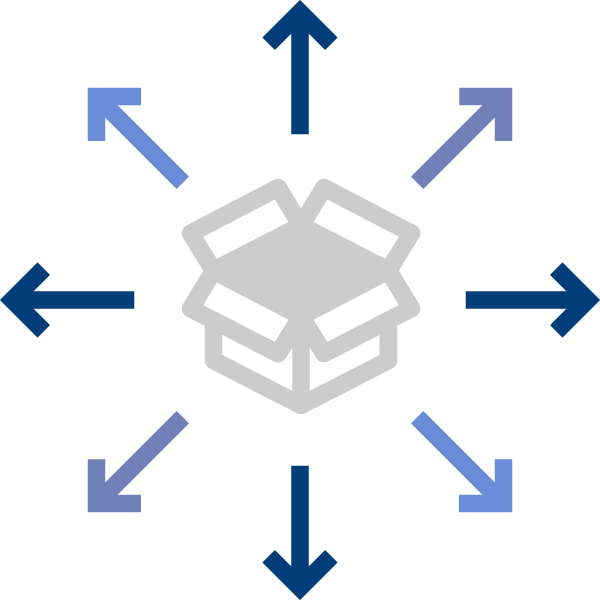
Q: More than three years out from the onset of the pandemic, are you still seeing manufacturers dealing with supply chain constraints?
A: Supply chain issues have not disappeared. In fact, we are still seeing certain industries, such as the automotive sector, continuing to struggle with component shortages and delays. As we add more and more electronics, advanced chips and circuitry into the devices used to control and operate vehicles, there is a greater need for complex parts, and it is harder to meet demand. Right now, we are seeing the continuing supply chain stress in highly technical industries requiring intricate engineering as the Internet of Things or IoT continues to grow. A year or two ago, the expectation was that these issues would have resolved themselves by now, but in some cases, they may be here to stay.
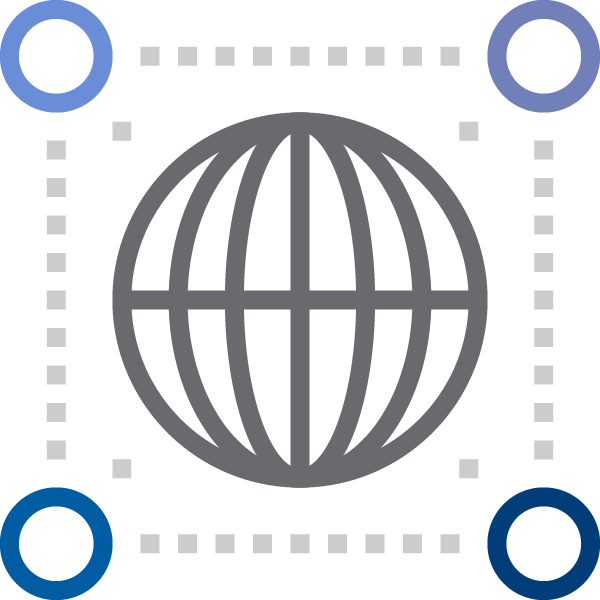
Q: Are you seeing manufacturers onshoring more of their operations in an attempt to streamline their processes?
A: Yes, we are seeing more organizations looking at onshoring to relieve supply chain congestion, mitigate risk with freight lead times and avoid repeating the kinds of issues we saw during the pandemic. However, not all manufacturers can flip a switch and move sourcing to the U.S. or Mexico. Redirecting distribution points and switching up supply chains entirely can take months or even years of research and refinement and, depending on the industry, require a significant level of approval within the customer base. Though manufacturing is back to pre-pandemic levels, the almost instantaneous shutdown of the supply chain in 2020 has had lingering effects. One of them is that it opened companies’ eyes to the need for greater redundancy with key suppliers at home and abroad.
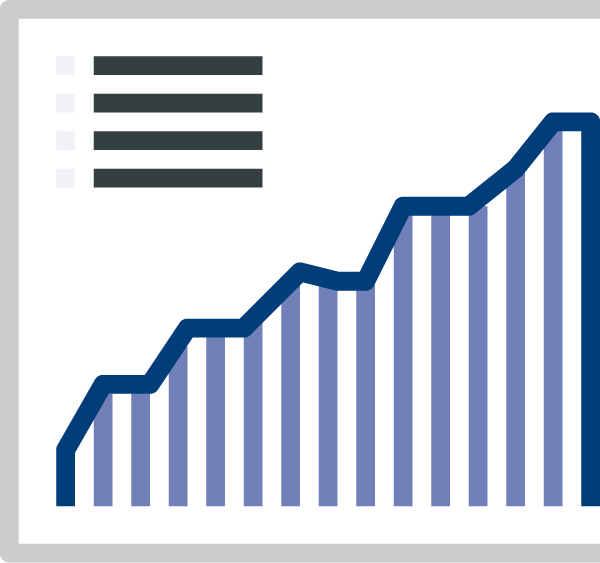
Q: What impact is inflation having on U.S. manufacturers and their strategies?
A: Earlier this year, when inflation was rampant, manufacturers were trying to keep their heads above water. The Fed’s aggressive approach has lessened the rate of inflation, and concern about tipping into recession has died down a bit. But input prices for labor and material costs are still a major cause for concern, especially among midmarket companies, who often have a harder time passing on price increases to customers.
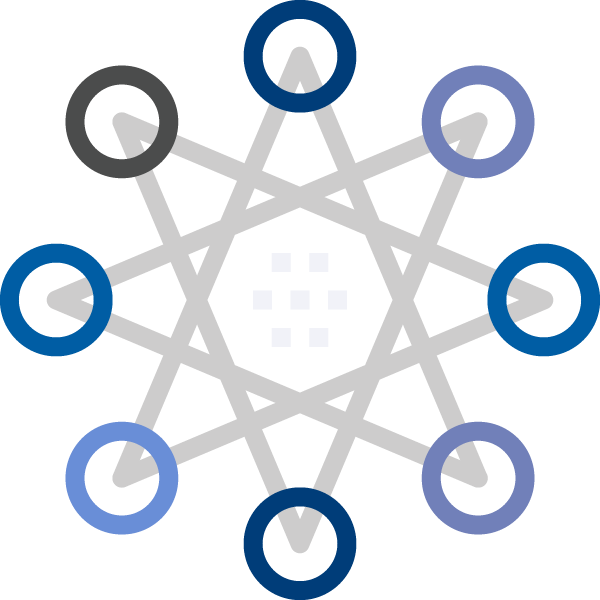
Q: AI has been one of the biggest stories of 2023. How have you seen it impacting manufacturing?
A: It’s pretty limited so far in the middle-market industrial landscape. It depends on the nature and sophistication of the manufacturing process. Clearly, AI has a role to play in supply chain optimization, process automation, defect detection, production, preventative maintenance and quality control. But it can require a significant investment and a high level of sophistication in the systems used both on the shop floor and in the back office to get it right. The more complex and automated the manufacturing process, the more likely the company would consider investing in AI.
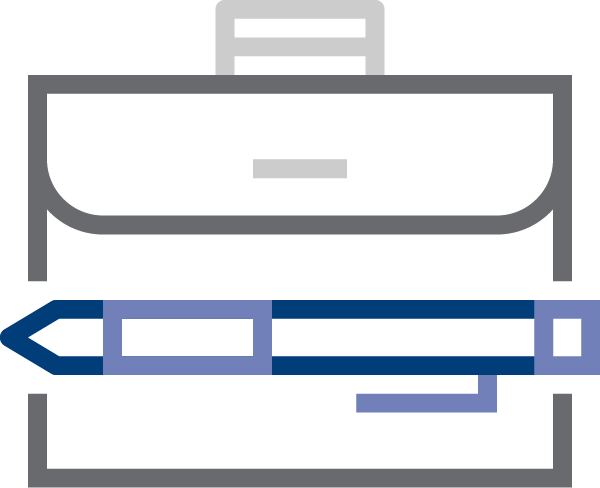
Q: What trends are you seeing in terms of talent recruitment in manufacturing?
A: Manufacturing has a long way to go in appealing to and recruiting younger generations. Approximately 15 million people work in the industry in the U.S.. However, there is a common misperception that robots have taken over a lot of manufacturing. Many jobs simply cannot be effectively or cost-efficiently performed by robots. We’re seeing companies launch programs to entice younger generations to get involved and better understand opportunities in manufacturing and how it can be a long-term career option. This includes partnerships with high schools and technical schools that can funnel people directly into jobs. The war for talent is intense and labor costs are rising significantly, especially in highly technical manufacturing businesses, which has also put additional pressure on companies to progress on the recruitment front.